Fallstudie: Drahterodieren als Alternative zur Bearbeitung von Profilen in Turbinenscheiben im Bereich der Luftfahrt.
ONA hat eine Studie zur Analyse von diesem Prozess des Elektroerodieren mit Draht (WEDM) als Alternative zur konventionellen Bearbeitung (Räumen) der Schlitze der Turbinenscheibe für den Luftfahrtsektor durchgeführt.
\Bearbeitung von Profilen in Turbinenscheiben durch EDM
Eine Führungsrolle im Sektor Elektroerodieren kann nur möglich sein, wenn kontinuierlich an der Erforschung neuer Technologien und Anwendungen gearbeitet wird, um fortschrittliche Lösungen zu bieten, die an den Bedürfnissen der Kunden angepasst sind. ONA ist ein klares Beispiel für ein Unternehmen, das sich in Richtung Innovation orientiert. Seine 65 Jahre Erfahrung in der Bereitstellung verbesserter Technologien für das Elektroerodieren garantieren dies. In Übereinstimmung mit dieser Philosophie hat das baskische Unternehmen eine Studie zur Prozess-Analyse des Elektroerodieren mit Draht (WEDM) als Alternative zur konventionellen Bearbeitung (Räumen) der Schlitze der Turbinenscheibe für den Luftfahrtsektor durchgeführt. Tatsächlich könnte das Drahterodieren von Schlitzen der Turbinenscheibe in der Zukunft eine praktikable industrielle Option zum Räumen werden.
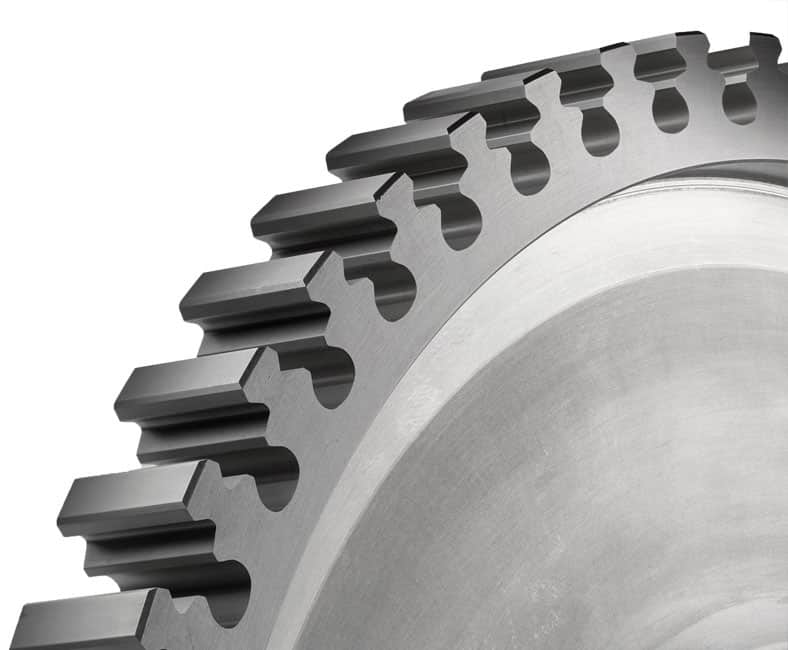
Annahme und Verfahren
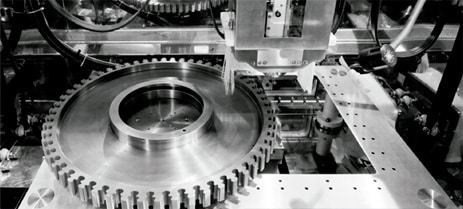
In seiner Forschung hat ONA das Verfahren für das Elektroerodieren mit den traditionelleren Bearbeitungsverfahren wie Räumen und Fräsen verglichen. Als Kernpunkte der Forschung vergleicht ONA Parameter wie Oberflächenintegrität, Präzision und Anforderungen an die Zeit für die Bearbeitung von Schaufeleinführungsnuten.
Für den Vergleich wurde eine Turbinenscheibe mit den folgenden Eigenschaften geschnitten:
- Material: Inconel 718.
- Außendurchmesser: 350 mm.
- 28 Plätze.
- Schlitze der Turbinenscheibe in einem Winkel von 30 Grad.
- Dicke 82 mm.
- Profil-Toleranz 0,01 mm.
- Toleranz radiale Winkelpositionierung 0,08 mm.
Ziel der Forschung ist es, die Zähne des Turbinen-Tannenbaums mithilfe der Technik für das Elektroerodieren mit Draht zu durchtrennen, um die Toleranzanforderungen zu erfüllen und so die folgenden Informationen zu analysieren:
- Geschätzte Zeit für ein vollständiges Profil.
- Zeit bis zum Beenden der Arbeit für ein vollständiges Profil.
- Gesamte Zeit Erosion für ein vollständiges Profil.
- Gesamte Zeit für das Schruppen der Turbinenscheibe (einschließlich Zeit der Vorbereitung).
- Gesamte Zeit für die Fertigstellung der Turbinenscheibe (einschließlich Zeit der Vorbereitung).
- Gesamte Zeit für die Bearbeitung (einschließlich Zeit für Konfiguration).
- Abtragsleistung Material MRR (mm2/min).
- Dicke der Schicht des geschmolzenen Materials.
EDM-Konfiguration und Bedingungen der Bearbeitung
Die Analyse wird mit der Standard-ONA-Technologie für Nickellegierung, einem 2-Achsen-Drehtisch und zwei verschiedenen Reinigungsbedingungen durchgeführt. Auf der einen Seite gute Waschbedingungen (geschlossene Düsen), andererseits schlechtere Reinigungsbedingungen (offene Düsen). Zusätzlich wird ein 0,25-beschichteter Draht für den Schruppschnitt verwendet.
Diese beiden für die Studie gewählten Szenarien (offene und geschlossene Düsen) ermöglichen die Durchführung verschiedener Tests, um die Zeit der Erosion am besten beurteilen zu können, da diese weitgehend von den Reinigungsbedingungen abhängt. Manchmal verhindern die geometrischen Eigenschaften der Turbinenscheiben den Einsatz des Elektroerodieren mit geschlossenen Düsen.
Sie sind besonders nützliche Modelle für die Herstellung großer Formen und verschiedener Kavitäten, was genau die Spezialität von Concours Mold ist.
Ergebnisse der Forschung
Nachfolgende Tests haben gezeigt, dass es mit der Drahterodieren-Technologie möglich ist, eine Schichtdicke beim Schmelzen im erforderlichen Mikrometerbereich (ca. 5 µm) mit ausreichender Präzision in den Schaufeleinführungsnuten innerhalb der Toleranz von 0,01 mm erreicht werden kann. Diese Ergebnisse wurden nach einem Schruppdurchgang und zwei Schlichtdurchgängen (3-Schnitt-Strategie) erzielt.
Unter schlechteren Reinigungsbedingungen (offene Düsen) beträgt die Abtragsleistungskapazität beim Schruppen 110 mm2 / min. Tatsächlich beträgt bei der in der Untersuchung verwendeten Strategie (ein Schrupp- und zwei Schlichtdurchgänge) die Abtragsleistung 60 mm2 /min.
Auf der anderen Seite ist unter guten Reinigungsbedingungen (geschlossene Düsen) eine deutliche Verbesserung des Abtragsleistungskapazität des Materials zu beobachten. Allein beim Schruppen erreicht sie mehr als 400 mm2 /min.
Kommentare auf der Grundlage der erzielten Ergebnisse
Bei den meisten Turbinenscheiben beträgt das Profil der Winkel 5 bis 30 Grad. Die konische Schneidfunktion der ONA-Erodiermaschine mit Draht erzielt gute Ergebnisse bei der geometrischen Präzision für Profile von weniger als 10 Grad. Für größere Winkel wird ein 2-Achsen-Drehtisch empfohlen.
Um den gewünschten Abtrag des Materials zu erreichen und die Zeit der Bearbeitung zu verbessern, ist es unerlässlich, das Dielektrikum im Erodierbereich zu reinigen. Es ist unerlässlich, die meisten Düsen im Profil geschlossen zu halten. Für Turbinenscheiben mit kleinerem Durchmesser (wenn die Düsen mit der Spannvorrichtung interferieren) wird die Verwendung von Spezialdüsen empfohlen.
Schließlich wird auch die Verwendung von beschichteten Drähten empfohlen, um den Prozess des Drahterodieren mit Draht zu reduzieren, insbesondere bei Schruppschnitten.
Schlussfolgerungen
Nach dieser Untersuchung können wir zu dem Schluss kommen, dass das Drahterodieren der Profile von Turbinenscheiben eine sehr gute Alternative ist, um mit dem Räumen als industrielle Lösung im Luftfahrtsektor zu konkurrieren. Die immer leistungsfähigeren Generatoren der neuesten Generation und die modernsten numerischen Steuerungen ermöglichen es, die Zeit der Bearbeitung zu optimieren und die Dicke der weißen Schicht zu reduzieren. Darüber hinaus bieten sie eine sehr gute geometrische Präzision.
In der von ONA durchgeführten Studie (3-Schnitt-Strategie) werden bei der Bearbeitung der Schlitze der Turbinenscheibe geometrische Toleranzen eingehalten, indem eine weiße Schicht unter 5 μm erreicht wird. Darüber hinaus erhält man wertvolle Informationen über die Abtragsleistungskapazität des Materials und der Zeit der Bearbeitung.
Es stimmt, dass die Zertifizierung des gesamten Prozesses des Elektroerodieren nach Luftfahrtnormen ein langer und kostspieliger Prozess sein kann. Aus diesem Grund kommt ONA zu dem Schluss, dass eine Kombination von Drahterodieren die beste Alternative für das Schruppen ist, weil es wirtschaftlicher und schneller ist, mit Räumen für die Endbearbeitung. Auf diese Weise ist eine wiederholte Zertifizierung von diesem Prozess nicht notwendig.