Unsere Strategie besteht darin, Luftfahrtunternehmen maßgeschneiderte Erodiermaschinen mit hohem Mehrwert zu bieten
INTERVIEW MIT MARIUS PETEAN, KEY ACCOUNT MANAGER BEI ONA
\ Kundenspezifische und hochwertige Maschinen für den Luftfahrtbereich
Die Entwicklung neuer intelligenter digitaler Generatoren war ein maßgeblicher Treiber dafür, dass sich das Funkenerodieren zu einem tragfähigen und äußerst wettbewerbsfähigen Fertigungsprozess in der Luft- und Raumfahrtindustrie entwickelt hat, selbst für sogenannte „kritische Teile“, d. h. rotierende Teile oder solche, die zyklischen Belastungen ausgesetzt sind und bei denen es zu Ermüdungseinbrüchen kommen kann. ONA spielt bei dieser positiven Entwicklung mit Beiträgen wie der AV35-Drahterodiermaschine für die Herstellung von Tannenbaum-Nuten in Turbinenscheiben eine wichtige Rolle.
Wie in dem Interview mit dem Key Account Manager bei ONA, Marius Petean erwähnt, besteht die Zukunft darin, sich weiterhin stark auf einen Sektor zu konzentrieren, der bereits 25 % des Jahresumsatzes der Firma ausmacht. „Alle im Luft- und Raumfahrtsektor wichtigen Unternehmen setzen Maschinen von ONA ein. Unser Geschäftsziel besteht darin, bei unseren eigenen Kunden in ihren verschiedenen Produktionsstätten weltweit sowie bei First- und Second Tier-Lieferanten, die EDM-Maschinen einsetzen, weiter zu wachsen, mit besonderem Fokus auf dem nordamerikanischen Markt“, fügt Petean an.
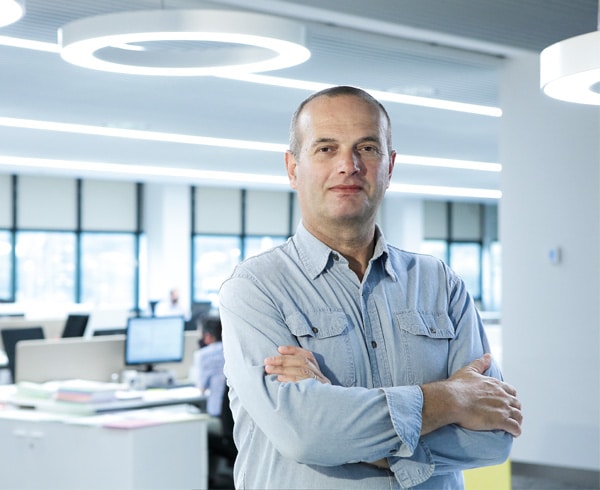
FRAGE. Wie begann ONA mit der Entwicklung von Anwendungen für den Energie- sowie für den Luft- und Raumfahrtsektor?
ANTWORT. ONA ist seit über 20 Jahren an Projekten im Luft- und Raumfahrtsektor beteiligt. Doch dies war lange Zeit in einem begrenzten Rahmen der Fall. Es handelte sich um Kunden mit einem Bedarf an Maschinen, die bestimmte technologische Anforderungen in Zusammenhang mit EDM-Bearbeitungsverfahren für Gasturbinenkomponenten erfüllen mussten. Noch vor 10 Jahren machten die Umsätze hinsichtlich der Luft– und Raumfahrtunternehmen weniger als 5 % des Jahresumsatzes von ONA aus. Dennoch erkannten wir vor nicht allzu langer Zeit die Notwendigkeit, das Management eines Sektors neu auszurichten, der den Umsatz steigern und gleichzeitig andere traditionelle Geschäftsbereiche wie das Formen und Stanzen für die Automobilbranche ausgleichen und diese ergänzen kann. Dieser neue Ansatz nahm vor 6 Jahren seinen Anfang. Seitdem wächst der Umsatz von ONA im Luft- und Raumfahrtsektor kontinuierlich und macht nun 25 % des gesamten Jahresumsatzes aus – mit der Perspektive auf eine deutliche Steigerung in den nächsten Jahren.
F. Könnte man sagen, dass EDM bereits die bevorzugte Technologie für die Herstellung bestimmter Teile mit einer komplexen Geometrie in einem so anspruchsvollem Sektor wie der Luft- und Raumfahrt ist? Ist das Verfahren im Hinblick auf die Qualität des Endprodukts mit Räumen und Fräsen vergleichbar?
A. EDM galt als in der Luft- und Raumfahrtbranche als ein „notwendiges Übel“. Bestimmte Komponenten können nur mithilfe von EDM bearbeitet werden. Aus diesem Grund haben Konstrukteure von Luft- und Raumfahrtteilen spezifische Verfahren zur Definition von Zeichnungen für solche Komponenten entwickelt, die sowohl EDM-Prozessanforderungen als auch Anforderungen an die Metallurgie- und Oberflächenqualität beinhalten. Das Funkenerodieren gilt als ein spezielles Verfahren, das vor der Anwendung in der Serienproduktion genehmigt werden muss. Dennoch hat sich diese Wahrnehmung in den letzten Jahren geändert. Neue EDM-Technologien auf der Basis modernster digitaler Generatoren ermöglichen nun einerseits eine erhebliche Steigerung des Materialabtrags und andererseits eine deutliche Verbesserung der erodierten Oberflächenqualität. EDM ist weiterhin ein „notwendiges Übel“, wird nun aber als eine praktikable Alternative für die Industrie gesehen, die andere Bearbeitungsverfahren ersetzt oder ergänzt. Beispielsweise macht die Oberflächenqualität, die gegenwärtig durch Drahterodieren erreicht werden kann, dieses Verfahren zu einer vollwertigen Alternative, um das Räumen von Turbinenscheiben zu ersetzen.
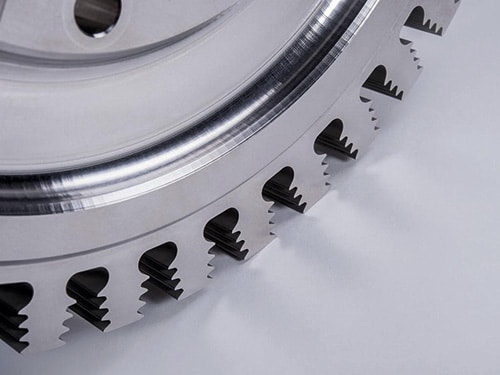
Zu den jüngsten Beispielen zählt ONAs AV35-Drahterodiermaschine für die Herstellung von Tannenbaum-Nuten in Turbinenscheiben.
F. Über welche Art von Teilen/Anwendungen reden wir da?
A. Die Palette an Luft- und Raumfahrtkomponenten und Anwendungen, bei denen EDM eingesetzt werden kann, wächst weiterhin. Existierten früher nur einige wenige Anwendungen, die fast ausschließlich dem traditionellen Erodieren vorbehalten waren, wie z. B. Kühlbohrungen und Vertiefungen in Leitschaufeln, Segmenten und Laufschaufeln, so werden diese nun in Laufrädern, integral ausgeführten Rotoren, Nachleitwerken, Turbinenscheiben, Brennkammern und Ventilatoren eingesetzt.
F. Was hat diesen Sprung in den letzten Jahren verursacht? War es die Entwicklung neuer Generatoren allein, die EDM zu einem wettbewerbsfähigen Bearbeitungsverfahren für den Luft- und Raumfahrtsektor gemacht hat, selbst wenn es sich um so genannte „kritische Teile“ handelt?
A. Der Technologiesprung wurde offensichtlich durch neue Generationen von Generatoren für Funkenerodiermaschinen, jedoch auch durch Fortschritte in der Entwicklung der EDM-Technologie ausgelöst. Konnten früher nur wenige EDM-Parameter konfiguriert werden, lassen sich jetzt mehr als 30 konfigurierbare Parameter einsetzen. Dies sorgt für eine viel größere Flexibilität, wenn es darum geht, die optimale Lösung zu finden. Zudem müssen wir die Arbeit der Erstausrüster bei der Einführung von EDM für kritische Komponenten anerkennen, das Engagement und die Hartnäckigkeit ihrer Konstruktions- und Fertigungsleiter, die offen und bereit waren, das Funkenerodieren für diese Art von Teilen zu akzeptieren, zu prüfen und zu genehmigen. Ohne sie wäre es unmöglich gewesen, diesen Punkt zu erreichen.
F. Welche technischen Vorteile bringen die neuen Generatoren für die EDM-Fertigung, beispielsweise von Gasturbinenscheiben, rotierenden Teilen, die bis zu 60.000 Umdrehungen pro Minute erreichen und extremen Druckschwankungen und Temperaturen standhalten müssen?
A. Bei den neuen Generatoren von ONA war es die Tatsache, dass sie digital sind. Jetzt können EDM-Technologien wie die Elektrolyse entwickelt und Mikrorisse reduziert oder sogar beseitigt werden, sodass ganz minimale harte Erodierschichten von nur wenigen Mikrometern erreicht werden. Die Oberflächenanforderungen sind akzeptabel und die Teile können für den Flugverkehr zugelassen werden.
F. Welche Vorteile bietet das Funkenerodieren bei der Herstellung von Teilen für die Luft- und Raumfahrt gegenüber traditionelleren Verfahren wie Räumen und Fräsen?
A. Aus industrieller Sicht wurden einige äußerst interessante Vorteile definiert, insbesondere beim Drahterodieren. Im Vergleich zur konventionellen Bearbeitung durch Fräsen und Räumen fallen die Kosten für wiederkehrende Verbrauchsmaterialien deutlich geringer aus. Im Hinblick auf das Räumen bietet EDM schnelle und kostengünstige Prototyping-Lösungen. Von der Entwicklung bis zur Herstellung eines Räumwerkzeugs kann es bis zu einem Jahr dauern, während das Drahterodieren fast sofort erfolgt und direkt mit der Programmierung des Schnittprofils verbunden ist. Darüber hinaus lässt dieser Ansatz keine Fehler zu; ist das Räumwerkzeug aus irgendeinem Grunde fehlerhaft, müssen Änderungen an der Konstruktion vorgenommen und ein neues Werkzeug hergestellt werden. Bei der Funkenerosion wird das Profil nach dem Schneiden des Werkstücks gemessen. Muss es angepasst werden, kann dies direkt durch das Programmieren des Schnittwegs erfolgen. Auf der anderen Seite stellt die Autonomie der Drahterodiermaschine einen weiteren großen Vorteil dar. Bei allen AV-Modellen von ONA besteht die Möglichkeit, ein 45 kg-Drahtspulensystem zu nutzen; dies ist fast 8-mal mehr als eine 8 kg-Standardspule. Und beim Senkerodieren lässt sich ein Trend zur Automatisierung mit Robotern sowie zur gemeinsamen oder individuellen Aufbewahrung von Elektroden beobachten.
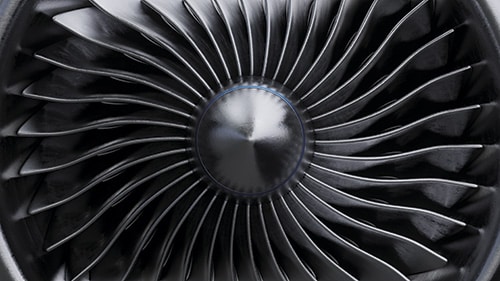
F. Gibt es bei traditionellen Bearbeitungsverfahren Einschränkungen, die bei EDM nicht existieren, wenn bestimmte Geometrien erreicht oder bestimmte Materialien bearbeitet werden sollen?
A. EDM ist ein berührungsloses Bearbeitungsverfahren. Es ist lediglich erforderlich, dass die zu erodierenden Materialien eine elektrische Leitfähigkeit aufweisen. Das ist offensichtlich ein Vorteil gegenüber der konventionellen Bearbeitung. Beim Erodieren von Aluminium- oder Nickellegierungen besteht fast kein Unterschied zwischen Materialabtrag und Werkzeugverschleiß (Elektrode), im Gegensatz zu der konventionellen Bearbeitung.
F. Welche Rolle spielt ONA bei der Entwicklung, das Funkenerodieren zu einer bevorzugten Technik für die Herstellung von Luft- und Raumfahrtteilen zu machen?
A. Wir arbeiten gemeinsam mit unseren Kunden, um spezifische Bearbeitungslösungen für ihre Bauteile zu finden. Wir suchen stets nach Lösungen für ihre Probleme und nutzen dabei EDM. Sagen wir mal, dass diese Annäherungsübungen zu interessanten und oft überraschenden Lösungen führen.
F. Also stellt ONA individuelle und angepasste Lösungen für die Unternehmen des Sektors bereit.
A. Ganz genau. Unsere Strategie in der Branche besteht darin, Kunden Lösungen mit einem hohen Mehrwert anzubieten. Wir hören ihnen zu und bieten gemäß ihren Anforderungen und ihrem EDM-Kenntnisstand individuelle Lösungen. Ein Beispiel wäre ein Kunde mit wenig Erfahrung im Erodieren, der uns um eine schlüsselfertige Lösung bittet, die die Konstruktion und Fertigung von Werkzeugen, EDM-Technologie, NC-Programmierung (numerische Steuerung) sowie die Freigabe von Industrieteilen beinhaltet. Zwei verschiedene Teilenummern und insgesamt neun verschiedene Erodierbearbeitungen.
F. Welche sind die neuesten technologische Anwendungen/Beiträge von ONA für den Luft- und Raumfahrtsektor?
A. Die jüngsten Beispiele umfassen ONAs AV35-Drahterodiermaschine für die Herstellung von Tannenbaum-Nuten in Turbinenscheiben, Drahterodiermaschinen für das automatische Schneiden aerodynamischer Profile zur Anpassung von Laufschaufeln an Ringe, Senkerodiermaschinen mit hohem Materialabtrag, Senkerodiermaschinen für komplexe Hohlräume in Bauteilen wie Laufrädern oder auch Senkerodiermaschinen für geformte Löcher in Lauf- und Leitschaufeln.
F. Sie sagten, dass ONA bereits 25 % des Jahresumsatzes in der Luft- und Raumfahrtindustrie macht, doch wie sieht die Prognose für die Zukunft aus?
A. Alle der im Luft- und Raumfahrtsektor wichtigsten Unternehmen setzen Maschinen von ONA ein. Unser Geschäftsziel besteht darin, bei unseren eigenen Kunden in ihren verschiedenen Produktionsstätten weltweit sowie bei First- und Second Tier-Lieferanten, die EDM-Maschinen einsetzen, weiter zu wachsen, mit besonderem Fokus auf dem nordamerikanischen Markt“, fügt Petean an.
F. Wo können wir die nächsten Innovationen bei EDM-Maschinen für den Sektor erwarten? Welche sind die nächsten Herausforderungen, um aufzuzeigen, dass die EDM-Technologie bei der Fertigung von Luft- und Raumfahrtteilen lebendiger ist als je zuvor?
A. Technologien und Verfahren erleben eine ständige Innovation. Mit der Entwicklung und Einführung neuer Technologien entstehen neue EDM-Anwendungen. Ein aufschlussreiches Beispiel ist das Erodieren für Schneidteile, die durch additive Fertigung hergestellt werden. Zukünftig werden wir nicht nur angepasste Technologien benötigen, sondern auch andere Maschinen, die besser auf die Art und Größe der additiv gefertigten Teile abgestimmt sind. Eine größere Herausforderung wird die Cybersicherheit von Maschinen innerhalb einer digitalen und vernetzten Industrieumgebung darstellen. Und ein wichtiger Mehrwert für die Kunden/Anwender von Erodiermaschinen wird die Maschinen- und Prozessdatenerfassung für die anschließende Analyse sein, um die Fertigungsprozesse sowie die präventive Wartung der Maschinen zu verbessern.